Cobalt For PE Paint
HS Code |
611287 |
Chemical Formula | varies based on formulation |
Color | typically blue - based on cobalt's coloring effect |
Density | specific gravity data available for formulation |
Solubility | soluble in appropriate solvents in paint system |
Viscosity Contribution | affects paint viscosity depending on amount |
Drying Acceleration | catalyzes paint drying |
Heat Resistance | offers some heat - resistant properties |
Lightfastness | has certain light - fast characteristics |
Film Hardness Contribution | increases hardness of dried paint film |
Chemical Resistance | improves resistance to some chemicals in dried state |
As an accredited Cobalt For PE Paint factory, we enforce strict quality protocols—every batch undergoes rigorous testing to ensure consistent efficacy and safety standards.
Packing | Cobalt for PE paint in 5 - kg packages, securely sealed for safe storage. |
Storage | **Storage of Cobalt for PE Paint** Cobalt for PE paint should be stored in a cool, dry place, away from direct sunlight. Keep it in a well - ventilated area to prevent the build - up of fumes. Store it in tightly sealed containers to avoid moisture absorption and contamination. Separate it from oxidizing agents and combustibles to prevent potential chemical reactions and fire hazards. |
Shipping | Cobalt for PE paint is shipped in well - sealed containers, ensuring no leakage. Shipment adheres to strict hazardous chemical regulations, with proper labeling. Transport is via approved carriers to ensure safe delivery. |
Competitive Cobalt For PE Paint prices that fit your budget—flexible terms and customized quotes for every order.
For samples, pricing, or more information, please call us at +8618136850665 or mail to sales6@liwei-chem.com.
We will respond to you as soon as possible.
Tel: +8618136850665
Email: sales6@liwei-chem.com


At the beginning, the research of pigments relied heavily on nature, but the color and durability were not good. Post-chemical industry gradually flourished, and craftsmen used their minds to study formulas, seeking pigments that were excellent in luster, toughness, and stability.
"Cobalt For PE Paint" came out after several years of grinding. The engineers studied the classics and participated in new techniques, which were tried and tested. At the beginning of this material, in PE paint, the color is bright, it does not fade for a long time, and it adheres very firmly. Since its advent, it has added color to the painting, added luster to the paint industry, and opened up a new path in the path of pigment, gradually becoming the most important in the world and becoming a temporary choice. Its development path is not yet exhausted.
On its chemistry, when it encounters various reagents, the reaction varies. In a certain acid solution, it may produce a slight blue, the color changes but the quality does not change drastically; when it encounters a strong alkali, the reaction is slightly intense, and the molecular structure may be easier. In PE Painting, it can stabilize its quality, increase its firmness, make the paint durable, sturdy and smooth. Exploring the physical and chemical properties of this object can be used in various industries, such as the essence of craftsmanship and the beauty of painting, all rely on its nature to get progress.
Today, there are products where cobalt is used in PE coatings, and its technical specifications are very important. The cobalt material used must be pure in texture and have fine impurities. In the refining process, the purity should be guaranteed according to the precise process. The content ratio should also be strictly controlled and in line with the established standards.
In terms of identification, the product should be marked with clear text, with the category and content parameters of the cobalt used. Users will know the details when they see it. In this way, the technical specifications and labeling are accurate, so that the quality of the cobalt used in PE coatings can be trusted, and it can also run smoothly in the city.
The reaction step is also crucial. The temperature is controlled in a specific range, so that the various substances can be fully combined, and the changes in color and texture can be observed, and the temperature should be adjusted in a timely manner. And it needs to be stirred evenly to ensure the consistency of the reaction.
The catalytic mechanism is indispensable. Choose a suitable catalyst and add it in sequence to promote the reaction quickly and effectively. In this way, after much tempering, we can obtain high-quality Cobalt For PE Paint, which is bright in color and strong in quality. It is suitable for all kinds of paint painting needs and adds a lot of color to the process.
View its chemical response, cobalt is in it, and it cooperates with various components to promote the formation of the reaction, so as to determine the color and quality of the pigment. However, the response of the old method may not be good, the color is uneven, and the quality is not strong.
As for the change of its nature, today's researchers have tried their best. Observe the matching of materials, adjust the temperature and time of the reaction, and hope to be able to change it. After repeated trials, it gradually becomes effective. The color is pure and bright, and it will not fade for a long time; the quality is solid and tough, and it can be adapted to various situations. This is all the power of chemistry, which makes things perfect, adds luster to work, and benefits the needs of people's livelihood.
Cover all things. Safety is the first, and the operation is regular. Today, when talking about cobalt used in PE coating products, its safety and operation standards are related to the well-being of everyone and cannot be ignored.
Cobalt used in PE coatings can add color and improve performance. However, this material is potentially dangerous. If it is not handled properly, the disaster will occur. Therefore, it is necessary to understand the importance of safety and abide by the rules of operation.
When storing, it should be placed in a cool and dry place, away from fire and heat sources. The seal must be strict to prevent it from contacting with air and moisture and changing. And it should not be stored with strong acids and alkalis to avoid violent reactions.
When taking it, it is necessary to wear protective equipment, such as gloves, masks, goggles, etc., to avoid contact with the skin and eyes. Weighing is accurate, according to the formula, and the dose cannot be changed without authorization.
During the preparation process, stirring should be slow to prevent it from splashing. The place of operation must be well ventilated to disperse harmful gases. If you accidentally touch it, rinse it with a lot of water as soon as possible, and in severe cases, seek medical treatment.
During construction, the site should be clean, free of debris, and well-lit. Construction personnel should be familiar with the process and follow the order. After using the utensils, clean them, and dispose of the residual materials properly. Do not discard them at will.
In short, cobalt is used in PE coatings, and safety and operation standards, such as two wheels of a car and two wings of a bird, are indispensable. Only by adhering to the heart of awe and strictly abiding by the norms can we ensure smooth production, healthy personnel and prosperous careers.
We study it to observe its properties and explore its changes. Cobalt is used in PE paint, which can adjust the drying speed of paint and change its quality and color. At the beginning, it is matched with various materials, observe its fusion state, and try it in different situations to test its tolerance. After repeated tests, we have obtained exquisite methods to make cobalt work well in paint, and the paint film is tough and radiant.
This Product Research & Development is not achieved overnight. All colleagues have worked hard, studying day and night, observing the methods of predecessors, taking the essence and removing the dross. Today has finally achieved success, and in the future, we should continue to improve, meet the needs of the times, introduce new ones, and expect the development of the paint industry to contribute to its growing prosperity.
After months of investigation, it has been tested by various methods. Looking at the surface of its application to the object, it changes with time, checking whether it dissipates harmful gases, and checking whether it penetrates into the substrate and has signs of toxicity.
Cobalt in PE paint, although it is an important agent for enhancing color and solids, its toxicity should not be underestimated. If people often touch PE paint containing cobalt or inhale its volatile particles, it may hurt the viscera and damage qi and blood. Therefore, when studying its toxicity, we must be cautious, find harmless alternatives, or control its use to ensure people's safety and well-being.
We expect it to reach a higher level in color stability, lasting for a long time, and will not be eroded by time. In terms of hardness, I also hope that it is very tough and can be honed in every way without damage. And may it become stronger in the road of environmental protection, leaving a pure land for future generations.
With time, when the technology is advanced and the cost is controllable, the cobalt used in PE paint products will surely be able to shine like a star, illuminating the fields of various applications, adding luster to the world and prosperity to the industry. This is the future prosperity we look forward to.
As a leading Cobalt For PE Paint supplier, we deliver high-quality products across diverse grades to meet evolving needs, empowering global customers with safe, efficient, and compliant chemical solutions.
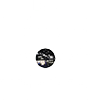
Scan to WhatsApp