Drying Agent (Polymerization Drier)
HS Code |
298538 |
Chemical Composition | Typically metal salts (e.g., cobalt, manganese, lead salts) in organic solvents |
Appearance | Usually liquid, can be clear or colored depending on the metal salt |
Solubility | Soluble in organic solvents like mineral spirits, turpentine |
Drying Mechanism | Accelerates the oxidation and polymerization of drying oils |
Activity Level | High - medium activity to speed up drying process |
Odor | May have a characteristic solvent - like odor |
Ph | Neutral to slightly acidic depending on formulation |
Flash Point | Varies, often in the range suitable for industrial use (e.g., 30 - 100 °C) |
Storage Stability | Good stability when stored in sealed containers away from light and heat |
Compatibility | Compatible with most common paint and coating resins |
As an accredited Drying Agent (Polymerization Drier) factory, we enforce strict quality protocols—every batch undergoes rigorous testing to ensure consistent efficacy and safety standards.
Packing | Polymerization Drying Agent packaged in 1 - kg bags for easy use. |
Storage | **Storage for Drying Agent (Polymerization Drier)** Store the drying agent (polymerization drier) in a cool, dry place, away from direct sunlight and heat sources. Keep it in a tightly - sealed container to prevent moisture absorption, which could reduce its effectiveness. Avoid storing near reactive chemicals. Ensure proper ventilation in the storage area to minimize the risk of fumes accumulation. |
Shipping | Drying Agent (Polymerization Drier) is shipped in well - sealed containers to prevent moisture ingress. Shipment is via reliable freight carriers, ensuring proper handling and compliance with chemical transportation regulations. |
Competitive Drying Agent (Polymerization Drier) prices that fit your budget—flexible terms and customized quotes for every order.
For samples, pricing, or more information, please call us at +8618136850665 or mail to sales6@liwei-chem.com.
We will respond to you as soon as possible.
Tel: +8618136850665
Email: sales6@liwei-chem.com


And later generations, the chemistry advanced day by day, and Zhu Xian began to think of artificial methods to create dry polymerization agents. After years of exploration, the formula process has become more and more exquisite. From the simple method at the beginning to today's exquisite agent, the change between them is beyond words.
The use of this agent has shown its ability in all industries, or to help paint dry quickly, or to promote polymerization reactions. The road to its development is actually the painstaking efforts of scholars and craftsmen of all dynasties, which has achieved today's prosperity and benefited everyone.
Look at its shape, either in the form of powder or in the state of granules, with pure color and uniform quality. When used, put it into the material and stir it evenly, it can exert its ability.
This product is widely used and indispensable in the paint and ink industries. With its help in drying, it can reduce working hours and increase efficiency. It is a good tool in the industry. Its stability, easy storage and transportation, is favored by many workers.
Manufacturing process, the first thing to do is to be careful about blending. The materials are put into the container in sequence, slowly stirring well, so that the fusion is seamless. Then heat up and control it with a moderate heat to make the reaction smooth. This reaction step should not be ignored, and it must be observed in time. If the temperature is high, it will be easy to spoil, and if the temperature is low, the reaction will not be complete.
After the reaction is completed, quickly set the cooling device and wait for it to set. After refining, remove impurities and keep them pure, and then become a good product. And when preparing, when a monitoring mechanism is set up, every step is carefully inspected, and any defects are corrected, so as to obtain a good treatment.
Looking at its chemical reaction, when polymerizing, it can urge molecules to form an orderly chain. Its response is also, like the combination of yin and yang, so that the monomers can be polymerized and the structure is gradually consolidated. If you want to be good, you must understand that the disturbance of various causes, temperature, pressure, and the amount of agent are all key.
As for modification, it is necessary to meet all needs. Or increase its stability so that it can last for a long time; or adjust its properties to suit different situations. It all depends on the researcher's insight into physical properties, ingenious methods, and turning the ordinary into the miraculous. With the aim of fine research, this agent can be used in the field of industry to develop extraordinary effects, help the chemical industry, thrive, and be used by the world for the benefit of people.
There is a desiccant today, which is called polymerization drier, which is quite useful in the field of chemical industry. The same name refers to this thing, although the name is different, but the meaning is the same.
The ancients said: "The name of the name is the real guest." The name of the polymerization drier is also the actual name. Or there is another name, it varies from time to time, place, and use. Although the name is special, the functions are similar, and they are all capable of promoting polymerization and drying.
This desiccant is made by chemical method, which can speed the drying of materials, and is indispensable in industrial manufacturing, paint printing and dyeing. The complexity of its same name is convenient for the industry, and it is also seen that this product is widely used and paid attention to. In chemical research, people must carefully observe the change of its name, so as to make good use of it and help the industry.
Qianzhai (polymerized Qianzhai) is a commonly used item in research. Its safe operation is very important, and it should be followed to ensure the benefit of the machine and the safety of people.
Anyone who uses Qianzhai (polymerized Qianzhai) must explain it in advance, and be familiar with its properties, uses and precautions. During operation, it is appropriate to wear anti-drying materials, such as clothing, gloves and eyes, etc., to prevent contact or damage to the eyes.
Store Qianzhai (polymerized Qianzhai), which is dry, dry, and well-connected, and has a good fire source, source and oxidation. Do not mix and store different Qianzhai to prevent backfire.
When using Qianzhai (polymerized Qianzhai), it is necessary to precisely control the dosage according to the requirements and avoid the dosage. If it is accidentally released, stop the operation immediately and clean it up quickly. Clean it up in a positive way to prevent powder from being damaged and inhaled.
After use, the remaining Qianzhai (polymerized Qianzhai) should not be mixed with ordinary garbage.
During the process, in case of accidents caused by Qianzhai (polymerized Qianzhai), such as burning, poisoning, etc., emergency measures should be taken immediately.
In addition, we can study commonly used things, but only by abiding by safety and operation standards can we ensure human safety and human interests.
In the past, such reagents were first developed, but their effectiveness was not yet perfect. However, the researcher has been very careful. After years of study, observing their physical properties and exploring their mechanisms, many formulas and preparation methods have been improved. Today's drying reagents have greatly increased their efficacy compared with past years, can meet the needs of all polymerization, and are more environmentally friendly and stable.
In the future, we should follow the path of improvement, hoping that its efficiency will be better, its application will be wider, and it will show more brilliance in the field of aggregation. It will contribute to all things in industry and industry, and help the industry continue to thrive.
We use scientific methods to observe this thing in detail. After repeated trials, we observe its response to various things, observe its volatilization state, and test its effect of entering the body. At first, the white rat was tested, fed with food containing this thing, and its appearance was observed day by day. Soon, the white rat gradually became tired and his diet gradually decreased. And flowers and plants were planted in the land containing this thing, and its growth was also hindered, and the leaves gradually wilted.
From this point of view, although "Drying Agent (Polymerization Drier) " has a significant effect on polymerization drying, its toxicity is also known. For industrial use, care should be taken to ensure complete protection from its harm and life, pollution and the environment. In this way, it can obtain its benefits and avoid its harm.
Looking at the future, its performance will be more refined. Or it can be achieved to high efficiency and quick drying, and it can be used in all kinds of complex situations to maintain stable effectiveness. Its application field will also expand. In addition to today's industrial fields, it may be able to enter emerging fields, such as fine electronics and green energy. In this process, it will be able to cooperate with other things to promote the leap of technology. Therefore, this product is expected to become an important tool in the chemical industry in the future, creating a new situation for our generation.
As a leading Drying Agent (Polymerization Drier) supplier, we deliver high-quality products across diverse grades to meet evolving needs, empowering global customers with safe, efficient, and compliant chemical solutions.
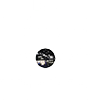
Scan to WhatsApp